Le Lean n’est pas adapté à mon entreprise...
Des chefs d’entreprise ont cette réaction et complètent leur propos par «je ne suis pas fournisseur de l’automobile» ou «De toute façon, je ne fais que de l’utilitaire». Clap de fin ! Plutôt travail d’explication pour PERFOLOR, groupement vosgien de six consultants qui offre un large panel d’expertises dans les domaines commerciaux, financiers, du management d’équipes, de la qualité et de l’amélioration continue. Cette réaction est plutôt liée à la peur du changement. Déployer le Lean Management, c’est modifier des habitudes de travail, …
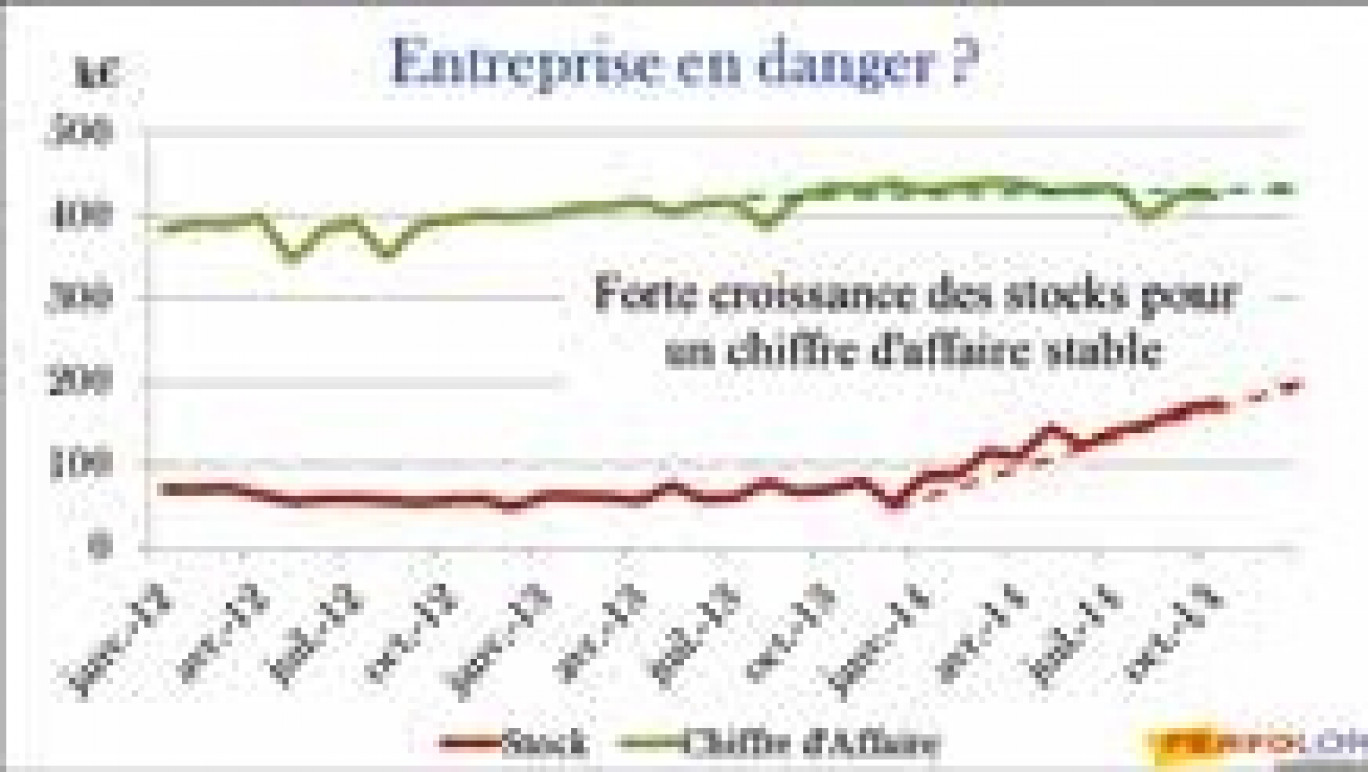
frédéric.jacquot
Se mettre dans l’instabilité de la nouveauté jusqu’à ce que chacun retrouve ses repères. Le Lean Management n’est pas une méthode mais plutôt une philosophie complétée par une boîte d’outils bien éprouvée par des leaders dans leur domaine, de la restauration à l’industrie automobile en passant par la construction navale. Si la célèbre marque américaine de fastfood maîtrise parfaitement le travail standardisé pour que ses hamburgers aient le même goût partout, l’industrie navale ne construit pas des bateaux identiques en grand nombre. Pourtant, les chantiers de Saint-Nazaire ont réduit par trois leur temps de fabrication et gagné 30 % de productivité en appliquant la même logique que celle utilisée pour associer tranches de pain, steak et sauce. Les navires ne sont qu’un puzzle de modules préparés à l’avance et assemblés comme un Lego®. Dans les deux cas, les différents flux d’information et de pièces ont été finement étudiés pour être simplifiés et synchronisés jusqu’à devenir un hamburger ou une ville flottante. C’est la mise en œuvre du concept de base du Lean : l’élimination des gaspillages. Les Japonais de Toyota qui ont structuré la démarche ont désigné sept types de gaspillages.
Les 7 Mudas
La surproduction : Produire plus que ce que le client achète et stocker des produits qu’aucun autre client ne voudra. Ils resteront chez vous sans valoriser le savoir-faire que vous avez fourni en les fabriquant.
Le transport : votre client ne paye pas les kilomètres que le produit a parcourus dans vos ateliers !
Les manipulations : le produit n’est pas vendu plus cher s’il a été posé plusieurs fois sur vos machines. Ces manipulations sont synonymes de port de charge avec toute la bobologie associée. Les réduire revient aussi à améliorer les conditions de travail.
Les attentes : «Il faut sortir de la pièce» dixit le chef d’atelier ! mais attention à la surproduction ! Équilibrer les postes, lisser la charge de chaque machine vous permet d’adapter les temps d’ouverture et de synchroniser les tâches pour que le flux de valeur soit continu.
Les rebuts : Jeter des pièces met mal à l’aise, mais refaire le travail déjà fait parce qu’il n’est pas correct doit faire réagir.
Les stocks : coûtent chers et accaparent une partie de votre trésorerie en cachant les véritables problèmes. Vouloir baisser les stocks doit conduire à une réflexion sur l’origine de ces accumulations.
Les tâches inutiles : sont souvent des actions ajoutées pour se protéger. Comment avoir confiance ? Cela passe par de nombreux outils bien au-delà du Lean et inclut la formation pour une meilleure maîtrise des outils.
Décrits ainsi, nous pouvons constater que les 7 Mudas sont présents dans toutes les activités. Alors le Lean Management s’applique partout mais sans être dogmatique. N’oublions pas que certaines activités doivent laisser une place importante aux rêves !